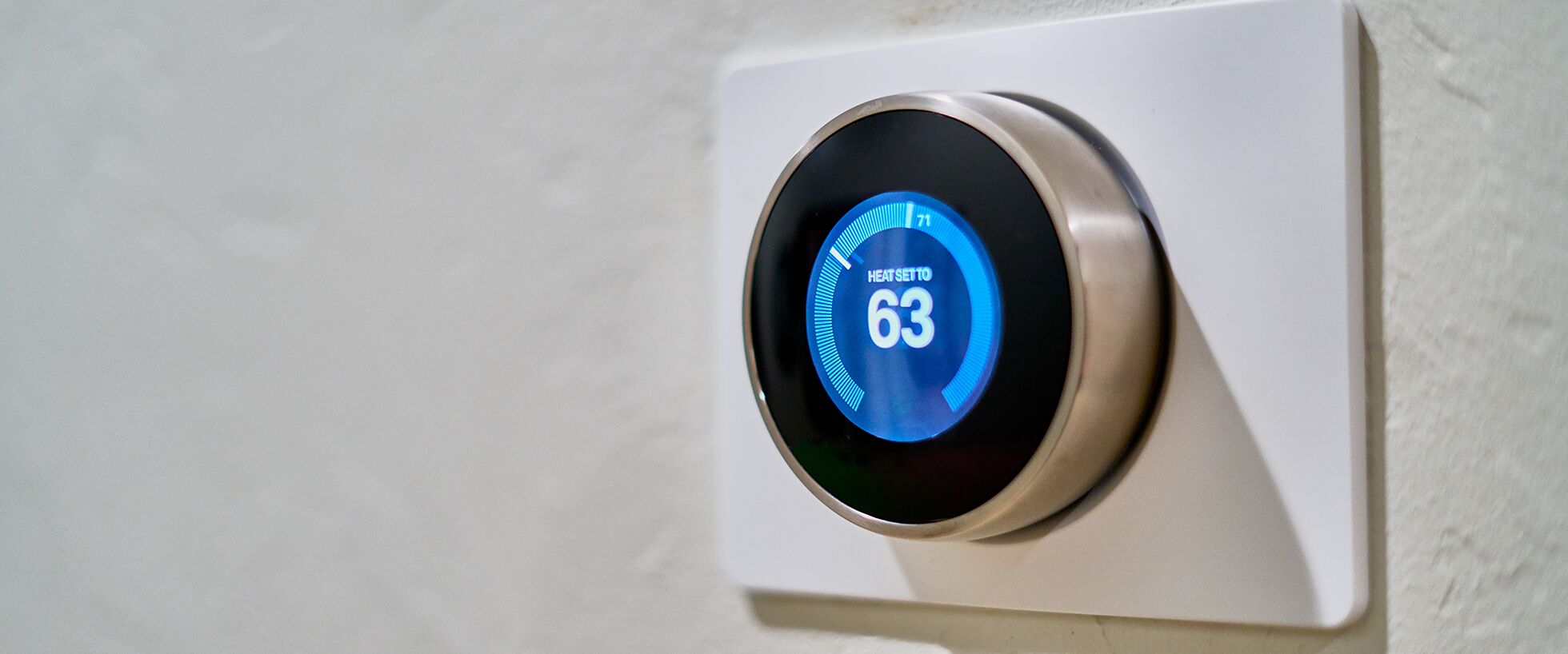
19 Mar The Internet of Things and the Purpose of Brands
The Internet of Things (IoT) has moved beyond the realm of prediction, conference panels and planning. It is no longer a future trend. It is entering reality at full speed. And it stretches way beyond what most people perceive when they hear or talk about this topic. Internet of things(IoT) much more than the “Home of Tomorrow”, where refrigerators are remote-controlled, the washing machine starts cleaning your clothes all of its own and the light bulbs are turned on before you arrive back home at night.
Most of what happens in Internet of things plays out beyond smart homes and lifestyle enhancement. It is about smart manufacturing and services as well as people who need new skills and a completely different culture to manage the factory of the future. This is why ABB, which sees itself as a pioneering technology leader that is writing the future of industrial digitalization, has developed an even wider concept it calls the “Internet of Things, Services and People” (Intern of things TSP).
Some experts and managers refer to “Industry 4.0.” Others are talking about “Industrial IoT.” Yet others prefer to discuss “Smart Factories.” In the end it is all about connecting industrial and office devices with each other via the internet or through company networks, making the entire factory floor – including its supply chain and customer communication – smarter, safer, more reliable, more sustainable, more responsive and thus more efficient, with less maintenance, less equipment failures and improved operations.
The main drivers supporting this historic transformation are obvious: Increased availability of data, programmable manufacturing machines, smart and low-cost sensors, more processing power, better connectivity, advanced software and the internet as an open platform. There is enormous potential out there for the adoption of the IoT. According to Gartner, the world’s leading information technology research and advisory company, more than half of major new business processes and systems will incorporate elements of IoT by the end of this decade. A Gartner survey in March 2016 promised “that 43 Percent of Organizations Are Using or Plan to Implement the Internet of Things in 2016.” This translated into an annual growth rate of 50 percent and nothing less than a “move toward mainstream adoption.”
Exploring ideas and concepts
Nevertheless, a close look reveals that the corporate world is very much at the beginning of its transformational journey from traditional manufacturing into this new digital era. Many companies have begun to explore ideas and future concepts for better space management, real-time quality control, cloud based planning platforms, reduced down times and higher system efficiency, as well as predictive maintenance and equipment monitoring, optimized cleaning intervals, or smarter use of human resources, to name just a few of the numerous valuable application areas.
Key competitors in many industries like automotive, chemicals, electronics, transportation and health – as well as their suppliers and customers – are aware at this point that they can´t afford to lose any more time to exploit the potential IoT benefits. DHL is researching ways to improve shipping and logistics with the help of IoT. General Electric cooperates with AirAsia to monitor the performance of airplane engines with the help of new sensors. Caterpillar is building monitoring systems for its construction vehicles with the help of Accenture. Industrial robot maker Fanuc has released new painting robots for cars and components in its quest to reach “Zero Down Time.” The robots collect data every 90 seconds while in operation in order to detect changes and predict maintenance issues. The data are extracted and analyzed automatically.
Big Data
Connecting devices, machines, facilities and people will create a massive amount of data. General Electric reports that its diesel/electric locomotives generate nine million data points per second. These data need to be stored, analyzed and translated into action in order to be useful. If they are handled well, they allow IoT companies for a better management of supply levels, forecasting, real-time monitoring of the manufacturing process, improved inventory readings, supply chain coordination – and much more. This is why experts are convinced that data lies at the heart of this whole new universe. Intelligent data analytics is a key precondition for a successful digital transformation of the entire production process. So building up the necessary capabilities and analytical routines is absolutely essential. But it will take years to make use of these immense data volumes in a way that leads to the right decisions.
A recent article in the British magazine “The Engineer”, titled “The top three trends driving the factory of the future”, stated that “We´re only scratching the surface of what can be achieved” in terms of big data. According to the American technology and services company “Aberdeen Group” the average IoT organization´s “total volume of data grew by 30% over the past year.” The report stated in early 2015 that “54% of IoT organizations reported that their current data analysis capabilities are insufficient.” But with data management moving from centralized storage to the edge of networks and into clouds, the task of utilizing big data won´t get easier. Ericsson is forecasting that there will be around 28 billion connected devices worldwide by 2021.
Challenges
Making good use of big data will allow for intelligent repair schedules, predictive maintenance, real-time monitoring and other forward-looking ways to improve operations. In the best case equipment failures can be detected before they happen. But the best preparation may not be enough when your network of devices and machines is connected to a wide-ranging supply chain or cooperation with partners who are not prepared that well. Fanuc knows from its customers that it´s often not the new robots that need attention – as the Nikkei Asian Review described it – but “other equipment such as conveyor belts, machine tools and inspection devices.” If devices in remote but connected factories are down, your own preparations are of limited use. Fanuc is now cooperating with 200 Japanese equipment makers and up to 40 companies in the US in order to network its operation monitoring.
Most companies apply machinery from dozens of different providers. So a huge amount of layers and devices needs to be coordinated across the factory floor. Various studies have revealed that suppliers without an Industry 4.0 strategy in place can be a real headache for some corporations. Not to speak of people and skills which are needed in order to implement the optimal Internet of things environment. “Our survey respondents say that their biggest implementation challenge isn´t the right technology, it´s a lack of digital culture and skills in their organization”, reported PricewaterhouseCooper´s “2015 Global Digital IQ Survey.”
People and their skills
Skills, culture and digital thinking will be an essential part of creating an IoT success story. It doesn´t help much if a company choses its perfect strategy and delivery model if the right people, or the matching culture, are not in place. Preparing the workforce in terms of training and mentality is necessary. Establishing collaborative and flexible approaches will be decisive. The growing complexity of networked environments and machine parks will require an increasing division of labor with cross-functional teams cooperating at the same time. An agile mindset is extremely important in this context.
But organization is not the only tool that will help to manage these challenges. The whole culture needs to change as well. Failure needs to be seen not as a flaw but as a value, like in Silicon Valley, because failures create valuable lessons in a constantly changing and multi-level environment. At the same time, parts of the control process will be taken over by machines and devices themselves but people will still be ultimately in charge. And they need to manage this increasingly complex interaction.
What does it all mean for brands?
“Even though it feels for most of us like we have arrived in the digital world quite some time ago, the transformation of the corporate world – especially in B2B – has only just begun. The shift to digital brings with it a mind shift, a people shift and a shift in expectations. The purpose of brands, though, remains unaffected”, explains Carina Hauswald, Managing Director at globeone Zurich.” Still, there are lots of opportunities for brands to improve their performance in this new industrial age. With better data, more efficiency, shorter ways to the market and better anticipated consumer tastes, brands will become more responsive. Based on more information, assisted by new communication channels and supported by a more flexible production process, marketing can become more effective. Digital relationships with customers will be deepened. And thanks to more tailor made and timely manufacturing methods individualization and customization of products can be immensely improved.
Also read Digital Transformation – The End of Branding as We Know it
Read more insights from Globeone
-
New Purpose Readiness Survey from Globeone
Most Swiss companies are well on their way to being at least partially credible for a purpose-d...
-
United against the coronavirus – examples of more or less successful corporate communication
The extent of the social and economic impact resulting from the global coronavirus pandemic is ...
-
Corporate Newsrooms – The organizational foundation for successful communication
If you had talked to communications managers about a “corporate newsroom” five years ago, they ...